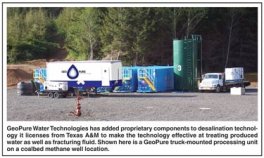
By Al Pickett Special Correspondent
The Barnett Shale, the granddaddy of domestic shale gas plays, is located beneath one of the most populated urban centers in the country: the Dallas-Fort Worth metroplex and its 5 million inhabitants. As if drilling and developing shale gas wells in this urban environment was not challenging enough, the region also is experiencing a drought.
That is significant because–as in shale and tight-sands plays in other parts of the country–Barnett wells require massive hydraulic fracturing to achieve commercial rates of natural gas production, and the slick-water fracs used on Barnett wells consume huge quantities of water. ion gallons of fresh water per frac stage, water has become a hot-button issue facing the development of shale gas plays from the Barnett in the Fort Worth Basin to the Marcellus in the Appalachian Basin.
In response, a number of solutions are emerging that use a variety of methods to recapture, treat, recycle and reuse the water from frac operations in shale and tight-sands gas plays.
“It is absolutely critical to responsibly and economically manage water, ” says David Crowe, president of GeoPure Water Treatment. “It is key to any development plan. There are so many intangibles to treating and reusing frac water, such as fewer trucks on the road, what happens to landowners, and service costs for operators. t pure water is not an unlimited resource.”
David Burnett, a researcher in Texas A&M University’s Harold Vance Department of Petroleum Engineering and director of technology for the Global Petroleum Research Institute in the Texas Engineering Experiment Station, points out that one large independent operator conducted a study in the Barnett Shale that showed frac operations were using only about 2 percent of the available freshwater.
“To put that in perspective, that is the same amount used by the area’s golf courses, so natural gas companies are not major users, ” Burnett notes. “However, in drought conditions, water can be shut off to golf courses. Oil and gas companies must position themselves so they are not competing for water. We do not want it to be an ‘either/or’ situation.”
Frac Fluid Constituents
According to Burnett, the constituents in the water used to fracture wells typically include a mixture of chemical additives such as a friction reducer (a polymer to reduce the viscosity of the water and improve its flowability to make it is easier to pump down the well), and a small amount of sand carried to the created fractures in the rock matrix to keep the fractures “propped” open during production.
Underground, Burnett says, the frac fluid picks up other contaminants present in the rock formation, including barium, calcium bicarbonate, iron, magnesium sulfate, sodium chloride and strontium.
Over the next several days, 70-75 percent of the injected frac fluid usually returns to the surface, with much of the remaining water eventually making its way into the well bore in incremental volumes as production operations commence. That fluid is then transported to saltwater disposal wells for reinjection into a porous rock formation beneath any freshwater aquifer zones, Burnett notes.