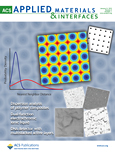
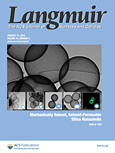
Figure 1. SEM micrograph showing a gap at the interface, that is, the absence of an interphase, between natural hemp fibers and poly-l-lactic acid (PLLA).
Recent studies pointed out that nanoscale cellulose is an interesting green reinforcing agent for the design of nanocomposites. Cellulose microfibrils can be extracted from wood or many other plant-based materials, but pulping and bleaching processes are not environmentally friendly. Cellulose whiskers can also be extracted from tunicate, a sea animal. Bacterial or microbial cellulose is produced by certain bacteria belonging to the genera Acetobacter, Agrobacterium, Alcaligenes, Pseudomonas, Rhizobium, or Sarcina, the most efficient producer of bacterial cellulose being Acetobacter xylinum. Acetobacter xylinum, an obligate aerobe, produces extracellular cellulose microfibrils to provide a firm matrix that floats and, therefore, allows the embedded bacteria to stay in close contact with the atmosphere. The produced cellulose pellicles play a great role in promoting colonisation of the cells on the substrate and provide protection against competitors. Cellulose pellicles were also observed to protect Acetobacter xylinum cells from UV light.Recently, Guhados et al. have measured the elastic modulus of single bacterial cellulose fibril using atomic force microscopy to be 78 GPa, which is much higher than those of natural fibers (generally less than 30 GPa) and is in the same order as that of glass fibers (70 GPa). This makes bacterial cellulose a very promising green nanoreinforcement.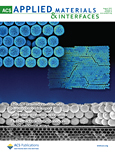
Materials and Methods
Materials Loose hemp fibers and mats were kindly supplied by Hemcore Ltd. (Hertfordshire, U.K.) and loose sisal fibers and mats by Wigglesworth & Co. Ltd. (London, U.K.). The cellulose producing bacteria strain Acetobacter xylinum BPR2001 (ATCC No. 700178) was purchased from LGC Promochem (Middlesex, U.K.). It was selected because of its high cellulose production capability under agitated conditions. Cellulose acetate butyrate (CAB-500-5 with 51% butyryl content, 4% acetyl content, and 1% hydroxyl content, w = 57000 g/mol, 1.14−1.28 g/cm3) was supplied by Eastman Chemical Co. (Kingsport, Tennessee, U.S.A.). a-Aldrich Company Ltd. (Dorset, U.K.).
Fiber Modification in Small-Scale Static Cultures Loose sisal or hemp fibers (0.5 g, 10 cm long) or fiber mats (4 × 4 cm) were put in 250 mL Erlenmeyer flasks containing 90 mL of culture medium which composed of 50 g/L fructose, 5 g/L yeast extract, 5 g/L peptone, 2.7 g/L Na2HPO4, and 1.15 g/L citric acid. The medium was formulated after H&S medium but with higher content of sugar and with fructose in place of glucose. This formulation was found to promote the production of bacterial cellulose with stable pH. After autoclaving at 121 °C for 20 min, the flasks were inoculated with 10 mL of a 3 day old broth of a previous culture of Acetobacter xylinum BPR2001. The fermentation was conducted under agitated conditions on a shaking plate (150 rpm) in an environmental chamber at 30 °C for one week.
Fiber Modification in an Agitated 5 L Fermentor Natural fibers were also modified in a 5 L bioreactor (BioFlo II, New Brunswick Scientific, Hertfordshire, U.K.) with air supply and pH regulation to pH = 5. The agitation was provided by two turbines. A round stainless steel cassette was designed and incorporated around the impeller shaft in order to store plant fibers or fiber mats inside the fermentor during the fermentation (Figure ). The cassette was not fixed to the impeller shaft so that it could rotate independently of the agitation speed, with two stoppers preventing it from moving along the shaft. Alternative to the use of the cassette, loose fibers (50 g, 1 cm long) were directly added to in the culture medium. The fermentor was autoclaved with 3.5 L of medium (same composition as above) with the filled cassette or loose fibers dispersed in the medium. The temperature of the fermentor was regulated to be 30 °C and the rotation speed set to 750 rpm. The fermentor was inoculated with 500 mL of a 3-day old broth of a previous culture of Acetobacter xylinum BPR2001.
Figure 2. Cassette designed to contain a natural fiber mat (or loose fibers) and schematic drawing of the fermentor vessel used.