Modern electronics depend on printed circuits. Instead of stringing physical wires between components, electronics manufacturers use metallic ink to print intricate patterns of hair-thin lines to conduct electricity and make devices like small antennas, RFID tags, and photovoltaic devices work.
The Laboratory of Applied Electronics and Communications is trying to improve the process of printing these tiny electronic circuits. LAEC is working on new ways to produce silver ink—not just shiny, but made of silver nanoparticles!—specifically for advanced aerosol-jet and inkjet printing tools.
One challenge in producing good metallic ink is producing smaller particles. Imagine each printed line on a circuit as your driveway: pour a bunch of boulders on your driveway, and you’ll have trouble getting to the mailbox. Pour gravel, and you get a smoother ride.
The same is true at the micro-level. We want metallic ink made of smaller nanoparticles to give a smoother, more uniform circuit trail for electricity to follow. The process we’re developing produces silver particles of 5 to 20 nanometers (that’s billionths of a meter). Our process works at room temperature and uses one less chemical step that other processes, meaning our process produces better circuit ink more efficiently.
Our smaller ink particles give our silver ink another advantage: lower curing temperature. If we want metallic ink to conduct electricity, we have to bake it onto the surface. That’s not a big deal if we’re printing circuits on hard substrates. But new applications require flexible substrates, like paper and plastic film. Apply high ink-baking heat to those flexible substrates, and the work goes up in smoke.
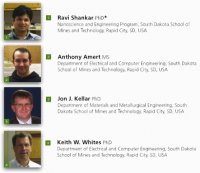
Baking temperature usually depends on particle size. The smaller the ink particles, the less heat we have to apply to make the ink conduct electricity. Our smaller nanoparticles thus widen the range of substrates manufacturers can use.
We face another challenge in getting these high-density particles to disperse in a stable solution. To make these nanoparticles flow like ink, we need to include a “ligand” in each nanoparticle, an extra chemical that makes the metal powder soluble. If that ligand remains after the ink is applied, it reduces the conductivity of the metal ink. So we need that ligand to stick to the metal enough to make it soluble, but not so much that we can’t remove it after we’ve applied the ink.